Знакомство студии с заказчиком началось с просьбы произвести оценку изготовления оснастки для проекта, выполненного другой компанией. После анализа собственными силами и с привлечением инженеров инструментальных производств было рекомендовано отказаться от существующей концепции ввиду нетехнологичности деталей, неудачного внешнего вида и чрезмерно дорогой стоимости оснастки для деталей, которые при грамотном проектировании могли быть значительно технологичнее. К сожалению, практически все решения в анализируемой разработке оказались неоптимальными, поэтому клиент принял решение начать проект «с чистого листа».
Работы по проекту условно разбиты на несколько этапов и представлены в хронологическом порядке:
- Подготовительный этап
- Рабочее проектирование
- Подготовка производства
- Сопровождение
Далее – повествование от первого лица.
Подготовительный этап
Как и любой другой, этот проект начался с планирования работ. Был составлен предварительный план-график, которому мы постоянно старались следовать, что не всегда получалось, однако этапность была полностью соблюдена.
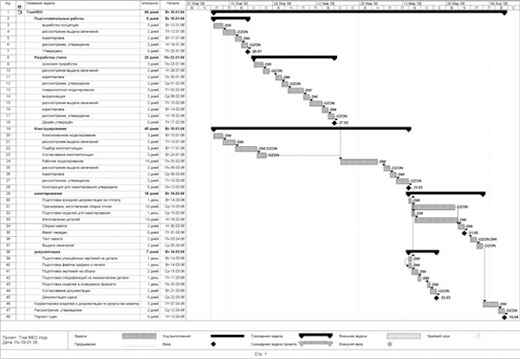
Рис.1: План-график
Следует подчеркнуть, что очиститель воздуха «Tree» не имеет аналогов. Это совершенно новая технология, и в процессе работы над прибором не останавливалась научная работа авторов технологии – американской компании Kronos Air Technology, вносившей несколько раз коррективы в технические требования.
Одним из условий успешной разработки является изучение возможных аналогов. Исследование конструктивных, компоновочных и стилистических решений, позволяет понять, что в каждом конкретном случае определяло то или иное решение, и чем оно хорошо или плохо.Поиск аналогов, как и следовало ожидать, ни одного прямого аналога не дал. Единственным относительно похожим прибором оказался воздухоочиститель Euromate VisionAir, предназначенный в основном для курительных комнат.
Любой курильщик мог видеть такие аппараты, например, в курительных комнатах аэропорта «Домодедово». Такой прибор был заказан и доставлен к нам, затем досконально изучен, с полной разборкой и анализом каждого элемента.
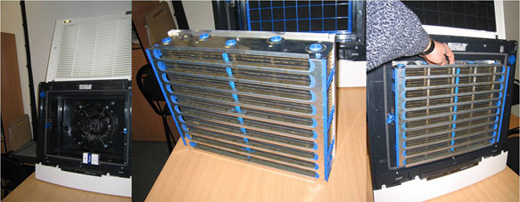
Рис.2: Анализ и исследование аналогов
В результате исследования были сделаны следующие выводы. Система фиксации картриджа была признана простой и надёжной, так же как и организация высоковольтных контактов между картриджем и прибором. Нам понравилась идея модульной стыковки двух приборов, которая затем была использованав модифицированном виде. Крепление крышки имеет неудачную конструкцию, при обычном пользовании крышка постоянно слетает со своих петель. К тому же, конструкция аналога оказалась неоправданно сложна и дорога в изготовлении. Поэтому было решено сделать крышку полностью съёмной, что значительно дешевле, проще и надёжнее.
Схема организации потоков воздуха не удовлетворяла требованиям, так как наш прибор, в отличие от аналога, не имеел механических нагнетателей (вентиляторов) и соответственно требовал организации потоков воздуха по схеме с меньшим сопротивлением. Поэтому наша конструкция картриджа не опиралась уже не на аналоги, а на технологию Kronos.
Также были изучены все демонстрационные технологические прототипы от Kronos. Поскольку наш дизайн-проект был первым для технологии и рассчитанным на массовый выпуск, прототипы рассматривались исключительно как компоновочные решения. После этого предмет разработки стал более понятен. Пришла пора заняться составлением технического задания, что и было сделано.
Рабочее проектирование
Этот этап начался с предварительного эскизирования. Эскизы выполнялись в программе векторной графики. Рассматривались любые теоретически реализуемые концепции.
Рис.3: Примеры вариантов 2D эскизирования
Получив все варианты эскизов, заказчик назначил совместные обсуждения, в результате которых была выбрана концепция для дальнейшего развития.
Следующий шаг – варианты компоновки. Здесь были приняты во внимание пожелания заказчика по разумной минимизации количества деталей. В тоже время было предусмотрено место для всех компонентов, заявленных в техническом задании и учтено их взаимное расположение.
Рис. 4: Пример вариантов компоновки
Утвердив у клиента вариант компоновочного решения, мы разработали концепцию построения основных элементов: картриджа, системы его фиксации, коронирующей рамки, ложемента и системы контактов. Был произведен расчёт компоновочных решений по воздушным потокам.
После построения математических моделей всего узла был создан сборочный прототип. В приборе присутствует высокое напряжение (порядка 16кВ), и далеко не все материалы, используемые в технологиях быстрого прототипирования, в состоянии выдержать такую разницу потенциалов. Однако мы смогли найти технологию, позволившуюя за разумные деньги и сроки получить полностью работоспособный прототип. Он отправился на испытания в Сиэтл, где их с успехом выдержал.
Рис. 6: Прототип рабочих частей перед отправкой в Kronos
И вот мы получили утвердительный ответ по поводу инженерного решения основного узла прибора. Располагая утверждённой компоновкой, учитывающей требования безопасности для высоковольтных приборов, мы смогли приступить к созданию стиля устройства: построению вариантов наружных поверхностей продукта и фотореалистичной визуализации. На этом этапе были достаточно жёстко определены все ограничения, поэтому варианты отличаются уже нюансами.
Рис. 7: Пример вариантов дизайна
Вариант для инженерного проектирования был выбран клиентом после расширенной презентации фотореалистичного качества.
Рис. 8: Финальный вариант дизайна
В процессе работ были созданы математические модели всех стандартных компонентов и новых корпусных деталей.
Рис. 9: Сборка, математическая модель
По просьбе заказчика в конструкцию прибора была заложена возможность полного обслуживания одной рукой. Также учтены все требования по защите пользователя от поражения электрическим током, что в последствии было подтверждено сертификационными испытаниями. Так в отсеке высоковольтной электроники вентиляционные пазы выполнены с лабиринтовыми выходами, не позволяющими коснуться металлической проволокой, вставленной снаружи, любых токоведущих частей. Фиксаторы крышки картриджа работают с усилием, не позволяющим открыть крышку ребёнку. В процессе разработки научная деятельность авторов методики не стояла на месте, поэтому в приборе появились дополнительные компоненты, например, датчики автоматического определения качества воздуха.
Конструкция прибора была утверждена по математическим моделям, наши инженеры подготовили и отправили разработчикам чертежи для разработки печатных плат прибора.
Рис. 10: Изготовление печатных плат американскими партнерами
Американские партнёры по проекту разработали дизайн печатных плат и изготовили опытные образцы для проведения испытаний. Одновременно с изготовлением плат в Сиэтле был получен прототип продукта, со,данный методом фрезеровки по нашим математическим моделям. После сборки и тестирования прототипа на собираемость и испытаний прибора, собранного на почти серийной электронике, были выданы рекомендации по небольшим доработкам конструкции. В частности, для минимизации помех, решено было перенести фиксаторы для прокладки кабеля дальше от платы управления.
Рис. 11: Рекомендации по изменениям
Итак, математические модели доработаны. Параллельно в Америке и в России создавались полнофункциональные прототипы. Американская версия – по технологии литья в мягкие формы (так наши партнёры смогли получить малую партию для расширенных испытаний). Русская версия – по технологии послойного синтеза, подтвердившей свои преимущества для прототипа рабочих частей.
Рис. 12: Полнофункциональный макет из силиконовых форм в Kronos
Рис. 13: Тестирование макета из силиконовых форм в Kronos. Двухмодульное исполнение
Рис. 14: Функциональный макет методом послойного синтеза в DW
В лабораториях Kronos были проведены расширенные испытания прототипов. Московский прототип также выдержал испытания. Удостоверившись в правильности решений, мы приступили к подготовке документации для серийного производства. Использование современных методов проектирования, плотный контакт с изготовителями оснастки позволили обойтись без плоских чертежей для всех пластиковых деталей проекта. По каталогу текстур и цветовому каталогу RAL, были выбраны варианты отделки наружных поверхностей прибора.
Рис. 15: Католог текстур, каталог RAL
Далее мы подготовили файлы печати символов на наружных поверхностях, собрали пакет информации для производства деталей, включающий в себя файлы математических моделей в экспортном формате, файлы печати и сопроводительный файл в котором были заданы материалы, текстуры и цвета на каждую деталь, а так же раскладка деталей по пресс-формам.
Рис. 16: Варианты цветовых решений
Подготовка производства
Подготовленная информация была разослана для оценки нескольким тулмейкерам в Европе и Азии. После получения коммерческих предложений, сравнения сроков и заявленного качества оснастки было принято решение изготавливать пресс-формы в Азии. Все вопросы, возникавшие при проектировании пресс-форм, оперативно решались совместными усилиями наших инженеров и инженеров фабрики, производившей оснастку.
Рис. 17: Производство отливок
Вся оснастка, несмотря на сложность, была изготовлена качественно. Часть пресс-форм была оснащена горячеканальной системой. Как показывает практика, у любого, даже самого качественного и дорогого изготовителя оснастки не получается с первого раза получить тестовые отливки без замечаний. Наш случай не явился исключением. После получения первых отливок были проведены полные обмеры и осмотр всех деталей, по результатам чего был составлен отчёт.
Рис. 18: Выдача замечаний по опытным образцам
По окончании доработок, повторного осмотра и обмера деталей, была отлита пробная партия деталей, которые были отправлены одновременно в Сиэтл и Москву. Используя детали пробной партии, в Kronos Air и в DesignWorks были собранны образцы для проведения очередного полного тестирования. После успешного прохождения всех тестов на предсерийных отливках, было дано добро на отправку пресс-форм в Россию.
Доставка пресс-форм осуществлялась сразу на литейное производство в Московскую область. Параллельно была заказана поставка материалов. После установки пресс-форм на термопласт-автоматы были отлажены режимы литья. Отладка режимов курировалась специалистами DesignWorks, на месте проводились обмеры и осмотр деталей. Стоит отметить, что процесс выхода на режим каждой формы и вся работа по сопровождению заняли продолжительное время – несколько недель. В итоге были утверждены образцы-эталоны для каждой детали и заказана их первая серийная партия.
Параллельно шла разработка упаковки. Требования к коробке предъявлялись жесткие, т.к. вес прибора составляет 8 и 11 кг, в зависимости от исполнения. Также была разработана оптимальная укладка всех упаковочных единиц, техническое описание на прибор, гарантийный талон и шаблон для разметки отверстий на стене при монтаже.
Рис. 19: Разработка дизайна упаковки
Сопровождение
Уже после старта серийного выпуска заказчик столкнулся с проблемой скорости сборки. Наши инженеры разработали и внедрили сборочные посты, оборудованные специально разработанными приспособлениями для разных технологических операций сборки.
Рис. 22: Разработанный сборочный пост
Кроме того мы порекомендовали поставщика комплектующих, который смог предоставить более выгодные для заказчика условия.
Максим Кондратьев
Team Leader
Источник: Designworks.ru
Зарегистрируйтесь или авторизуйтесь, чтобы комментировать